
Method Overview
We will be using bricks of agriculture waste as substrate, which will then be inoculated with fungus from grain spawn. All materials must be sterilized in order to prevent contamination. As the mycelium breaks down the nutrients, it establishes a matrix of substrate and mycelium which is strong and light-weight. The bricks will then be heated to stop the growth and dry out the material. These bricks can then be used to build structures, solidified through the process of bio-welding. The structure will then be coated in order to protect the bricks from degradation and contamination.

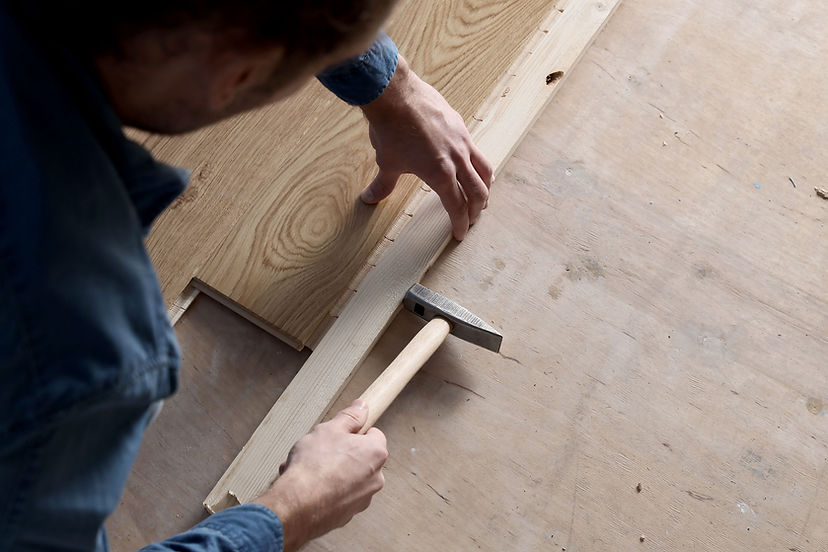

Building Plans
During week 4, we plan on constructing some devices that will help prepare and contain the substrate and mycelium bricks. Below are sketches of our initial design ideas.
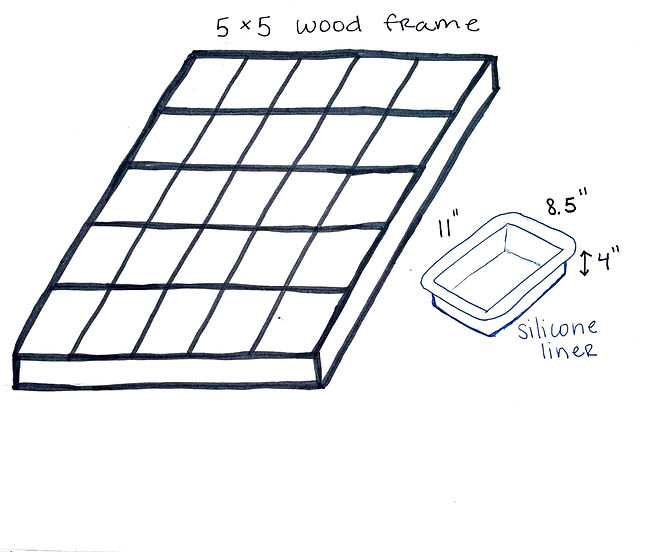
Wood Frame
We will construct a wooden frame that can contain 25 bricks while the mycelium grows through the substrate. Each brick will be approximately 8.5" x 11" x 4" and will be lined with a silicone mold to easily remove it from the frame. A large tarp will be secured over the frame in order to retain moisture and desired growing conditions for the mycelium to grow.

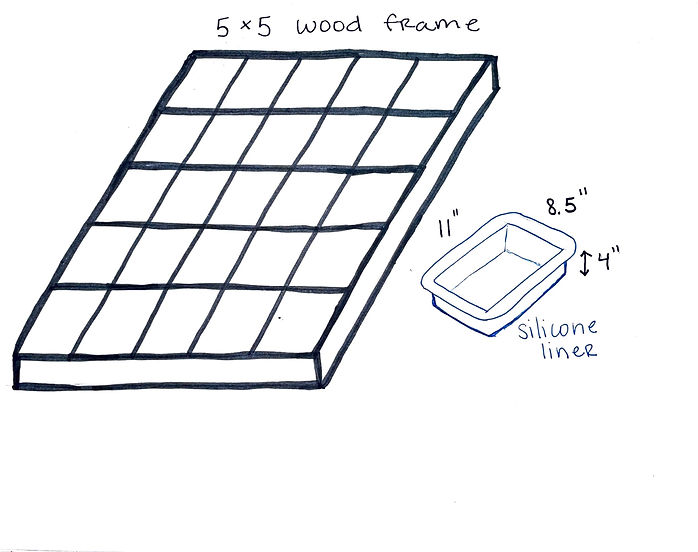

Substrate Straining Device
Before the substrate can be inoculated, it must go through the process of pasteurization in order to sterilize the material. This causes an excess amount of moisture, so water must be strained from the substrate before it is placed in the grow mold. The substrate will be pressed (using clamps or weights) between coated plywood and a mesh screen. The water can be captured and reused in other farming practices.
Substrate Recipe
Components:
-
coconut coir (agriculture waste)
-
oat bran (dense nutrients)
-
gypsum (mineral that helps retain water)
-
grain spawn (nutrient dense wheat berry + mycelium)
Ratios:
1gk coconut coir: 0.118 kg oat bran: .046 kg gypsum
2 parts substrate mixture (pasteurized): 1 part grain spawn, distributed evenly

Research
Past Mycelium Brick Trials
At the University of Oklahoma, Tayana Ghosh, an architecture graduate student, developed a new sustainable building material mixing mycelium fungus with recycled glass materials. Through her research, she has done a series of compression tests to make sure they can hold up. The reason for using glass instead of other materials is that they wanted the brick to have a reflectance property about it. She wanted to be able to pass light through the mycelium brick.
The process starts off by collecting agricultural waste and mycelium. The agricultural waste can be sourced from local farms. The waste is then sterilized and the mushroom grain spawn is added to the material. It's then dehydrated in the oven. She found it difficult to sterilize molds made from paper, plywood, foam, chipboard, and plaster. Through her experiments, she concluded that mycelium should not be compared with high-strength materials like wood, bamboo, or concrete. She suggests that mycelium materials can be used for insulation boards, sandwich panels, and acoustic board panels.
The main advantages of using mycelium are that it is a natural adhesive, it uses available raw materials, is low-cost has less construction expertise, and has a short manufacturing time.
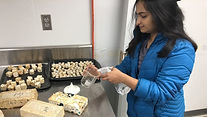



Ecovative is a company that specializes in mycelium technology that designs and grows sustainable materials. Ecovative mainly uses corn stalks as their substrate. They use mycelium to create foam, leather, beauty products, packaging, and different recipes using mushrooms. Every product that is made is able to compost back to nature, creating no waste. They have two main processes they do, MycoComposite, and AirMycelium. MycoComposite uses farming and forest waste with the mycelium. This process creates eco-friendly packaging protection that can be composted at the end of their life. AirMycelium uses fungal fibers to create materials for food and fashion.
______________________________
An artist and co-founder of MycoWorks has had success in building and making art with mycelium. He used reishi fungus and sawdust substrate to grow bricks. As the mycelium grows, it converts cellulose in the sawdust into chitin, the same fiber that makes up insect exoskeletons. Once dried, the bricks have structural strength comparable to cement.